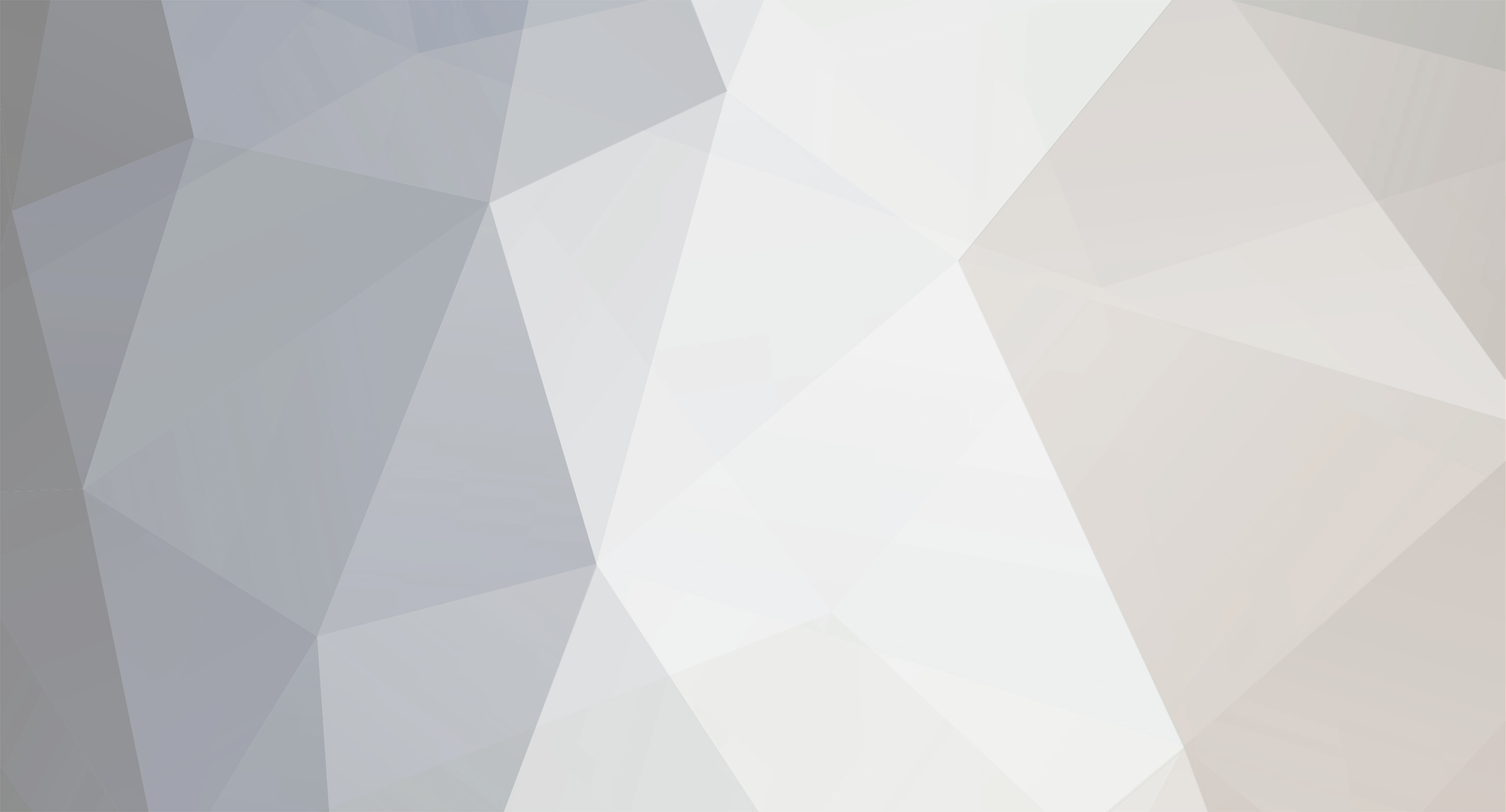
walkercope
Members-
Posts
21 -
Joined
-
Last visited
-
Feedback
0%
Profile Information
-
Location
Atlanta
Converted
-
First Name
Cope
-
Last Name
Walker
Recent Profile Visitors
422 profile views
-
-
walkercope reacted to a post in a topic: Improving hookup ratios
-
walkercope reacted to a post in a topic: Improving hookup ratios
-
walkercope reacted to a post in a topic: Improving hookup ratios
-
flaswimbaiter reacted to a post in a topic: Improving hookup ratios
-
Wondering if anyone's got advice on improving hookup ratios - We've been on a good striper bite but of ~12 eats I've gotten so far I've only hooked 6 of them good enough to land. Most fish have been 20+lbs and I'm fishing 10" glides. Should we go up a size in hooks? Is there a general guideline on hook size vs lure thickness? Using 1/0 ST66's for now. PFA with @nagatoro
-
nagatoro started following walkercope
-
walkercope started following nagatoro
-
walkercope reacted to a post in a topic: ISO Dockrat 10" trout
-
for sale Dockrats, deps, toxic, rago, mattlures, trapbass, pb rat, nez
walkercope replied to Metalhead79's topic in Black Market
-
I've casted off a few baits in the last couple years - luckily only one resin bait but trying to switch up my terminal tackle game this year. Have been doing straight 65 lb braid tied to lure with a modified uni knot. I'm thinking I'll switch to a new knot and use a snap - maybe san diego jam and #5 decoy egg snaps. But wanted to get people opinions. I'm fishing for stripers in a river with a good bit of structure so I keep the drag tight all the time. So whatever I use needs to hold up to some big head shakes and the occasional snag during a cast. Mostly fishing baits in the 5oz range
-
walkercope reacted to a post in a topic: KGB chadshad
-
-
Yeah makes sense. Fluid analysis is way above my intelligence level lol so I'm good with trial and error for that. Also your advice about simplifying it to center of volume vs center of mass is really helpful. I don't know why I was thinking I'd need to consider all the individual forces independently...so that gives me an easily obtainable goal so thanks!!!
-
I've read that it's possible to model that too by creating a shell around your model with the expected clear coat thickness and density but I felt like trying to factor that in for now was a bit more than I'm ready to try to handle. So I think I'm just going to pour some blanks and see how it goes. Maybe I'll decide that I need a tuning chamber in the future...
-
Yeah my plan is to have the COM below the COV, I think we're in agreement there. I guess there's two questions I have though: a) the first question I asked - overall body density vs sink rate? b) the distance needed between the COM and COV to keep the bait oriented vertically at all times, when burning it and twitches etc? Like for example looking at a hypershad, it's really impressive how stable it is even when they burn it real fast, and that's what I'd like to achieve ideally. I'm considering trying to mold in foam cylinders to the top of the bait to move the COM down further. But I think for now I'm going to try it without the foam and see if it's good enough without to keep it simple. Theoretically though it seems like if your COM is below your center of the drag force then the bait would tend to nose up. I'm thinking by spreading the weight out along the length of the bottom of the body I could limit that by giving the bait a high moment of inertia in that axis?
-
Oh man I'm not even thinking about paint or clear coats yet. If you have any suggestions I'd love to hear.
-
Yeah I'm an engineer too. I'm not sure that it'll be ok to combine the gravity force and the buoyant force though because the center of the buoyant force needs to be vertical above the center of the gravity force pulling down. If I had some flow analysis software that would be fun to try but I'm not about to pay 30k for a license lol.
-
danthefisherman reacted to a post in a topic: Density Vs Sink Rate
-
@danthefisherman I guess it's a bit misleading to just say "density" of the bait - what I'm calling the density of the bait (I'm making a two piece glide), is the mass of the whole body, including resin, screw eyes, ballast, hook, split ring, swivel, and anything else in the body, divided by the volume of water it displaces (for each of the two bodies individually). So this covers most things you mentioned. It's reasonable to account for all of these things in CAD since I can model and assign material properties to each piece and combine into a body. Also, I guess I'm trying to achieve the proper ballast and buoyancy with an internal harness that will get poured into each bait and located via mold features, hopefully so that I can just use featherlite without mixing in extra microbaloons (which I believe are pre-mixed into featherlite) If you're carving a master and molding it, then the iterative process you guys are describing seems like the only option but since I've already got my bait modeled in CAD, it tells me the mass, volume, center of mass etc for each individual body so I think I can have CAD do the heavy lifting for me.
-
walkercope reacted to a post in a topic: Density Vs Sink Rate
-
Obviously I could spend the time and money to mold a bunch of baits and vary the densities and measure the sink rates and come up with the relationship myself, but someone out there has already done it and has the answer. My bait will act a bit differently than theirs based on the shape but it will be in the same ballpark.
-
Keep in mind that using less dense resins will make your bait significantly more buoyant. If you want a specific sink rate then you are constrained by water displaced by your bait (the volume) - you have to keep the same density (mass divided by volume) overall. But using lighter resins and more ballast will make it more stable. Look up Archimedes' principle for more info. I'll be pouring my first bait soon-ish and am planning to use smooth-on featherlite which is much less dense than water after reading other threads where people have recommended it. I believe the resin you're using is a bit more dense than water?
-
I'm using smooth on featherlite which is 67% as dense as water, so it will float. I've done the math to see how much ballast I need to achieve a given % difference in density (object mass divided by volume of water displaced). The problem is I don't know what % increase in total mass of the body compared to mass of the displaced water to achieve the sink rate I want.
-
walkercope started following Density Vs Sink Rate
-
I'm wondering if anyone's done any tests to come up with a rough relationship between density and sink rates for swimbaits that they could share. I've finished modeling what will be my first glide so I know the volume and also the density of the resin I'll be pouring, so it's theoretically possible to get it right first try, but I'm not sure what relative density I should shoot for to get a ~1ips sink rate. I'm aware that shape also plays a big factor in this but the shape should be similar enough between baits that the relative density to sink rate should be extremely similar. Looking for something like "2% more dense than water gets 1ips"